to: Variable speed drive Restoration
in Category: VSD Wiki
- Products
-
- VSD Wiki
- Contact us
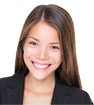
VSD manufacturers
sales@VariableSpeedDrive.co.za
Post Comments
<- - Back to Variable speed drive Restoration - ->
Restoration of variable frequency drive that have been exposed to excessive moisture or have been in a flood pose a more difficult challenge. A typical variable speed drive contains a wide range of operating voltages and power supplies, complicated printed circuit boards and intricate control circuits. The severity of damage to the variable speed drive usually will depend on whether or not the variable speed drive was operating when the exposure occurred. The damage that occurs is most likely more severe if exposure occurs while the variable speed drive is operating. If the variable speed drive is exposed while it is not energized, the damage can be less severe but will usually be latent in nature. In either case, if any input line or internal power supply fuse is open or significant corrosion is present, contact the manufacturer for specific corrective measures.Restoration should include testing or replacement of printed circuit boards or power semiconductors and the cleaning and drying procedures outlined below. In all cases, the manufacturer should be consulted for specific advice or details needed to restore the variable speed drive. Restoration should only be done by qualified technicians.
Cleaning. If nameplate information and other identifiers are not metal stamped and are still legible, record the information separately for future reference.
Disconnect and remove all printed circuit boards, clean and dry per the procedures outlined below, and re-install. Ensure all connections are labeled or marked for re-installation. Follow all applicable electrostatic discharge precautions. If the variable speed drive has an unsealed electronic current sensor, disconnect and remove it, and follow printed circuit board cleaning and drying procedures.
The remainder of the variable speed drive (transformers, chokes, fuse blocks, terminal blocks, heat sink, power semiconductors, power resistors, wiring harnesses, cabling, contactors, chassis, and cooling fans) should be washed down and scrubbed taking care not to damage insulated or brittle components. A solution of mild soap and hot water may be used as long as it is rinsed off with clean water. Water pressure should be limited to 25 psi. An approved solvent (as mentioned earlier) should be used for a final cleaning of insulating surfaces, contact tips, and magnet pole faces. Steam cleaning should not be used except on cabinets and enclosures from which the interiors have been removed.
Drying. Drying in the sun (without printed circuit boards) or in a warm room will take two to four days. If heat is used for drying, it should be limited to 212 F, preferably starting at 150 F and gradually building up to 212 F. Thermostatically controlled drying equipment must be used. Approximately 24 hr drying by this method should generally be sufficient.
Lubrication. All mechanical joints, sliders, bearings, and moving parts should be cleaned and lubricated per the manufacturer's instructions. No oil should be applied to contact surfaces or magnet pole faces.
Thermal compound check. Disconnect one or more power semiconductors and remove for inspection of the thermal compound layer (heat sink grease) to ensure water has not displaced or contaminated the thermal bond between the mating surfaces. Re-apply thermal grease to the power devices in accordance with the manufacturer's recommendations, and re-install the power semiconductor devices. This must be done with all power semiconductors if any show signs of contamination.
Coils and transformers. Wash with clean warm water and dry by any of the methods previously listed. Magnet armatures should be in the open position or the coil should be removed from the magnet. For drying dc coils by this method, a resistor in parallel with the coils is recommended to provide a discharge path for the kickback voltage that is induced when the circuit is opened. Special care should be taken to dry out dc coils, because in operation the inductive voltage may be several times the normal voltage. Disconnect wiring and check with a megger (500 V maximum) for a minimum of one megohm resistance.
Contact surfaces. Clean all contact surfaces with an approved electromagnetic component cleaner. Filing the tips is not recommended but may be done if the surface is very difficult to clean. Do not use sandpaper or emery cloth, which would deposit grit on the tips. Particular care should be taken with small contacts such as electrical interlocks, overload relays, and push buttons.
Insulating parts. All surfaces should be cleaned with an approved cleaner, particularly between poles, and dried carefully. Surface drying is generally sufficient for glazed porcelain, Melamine, and non-absorbent plastics. Unglazed porcelain (including power resistors), Bakelite, and Rostone absorb water and should be baked to dry thoroughly.
Thermal overload relays. Melting alloy type relays should not be disassembled. Clean and dry external parts only. Clean heater surfaces to permit normal heat radiation. Bimetallic type overloads should not be taken apart because of their intricate assembly. For emergency service, they can be used if they check satisfactorily mechanically and electrically.
Printed circuit boards. Follow all applicable electrostatic discharge precautions when handling printed circuit boards. If any of a printed circuit board's labeling is still legible, record the information separately as the cleaning process may destroy this information. Immerse the printed circuit board in a solution of mild soap and hot water and scrub gently with a soft brush. Rinse the printed circuit board in hot clean water and either blow it dry using filtered low pressure air or follow the general drying procedures outlined previously. Do not sun dry printed circuit boards since some components may be sensitive to ultraviolet (UV) radiation. If the printed circuit board has batteries to support its memory, check that the battery has not been excessively discharged. Consult the variable speed drive manufacturer for guidance if necessary.
Power capacitors. Inspect all power capacitors for leakage or compromise of the case of the capacitor. If the capacitor has a pressure relief plug, ensure its integrity is intact. Individually test each capacitor for proper electrical characteristics.
Bus work. Inspect all bus work in the variable speed drive to include inspection of each joint held together with bolts or other fasteners. Ensure each joint is clean and is re-assembled and torqued to the manufacturer's recommendations. This includes all cables that are connected to this bus work via terminal lugs.
Conduit. All conduit runs to and from the variable speed drive should be inspected to ensure no moisture is trapped in low areas of the conduit run or in any of the junction or connection boxes.
Final check. Motor must be disconnected from variable speed drive for this check or damage can occur to the variable speed drive. Test the insulation resistance of the motor cables with a megger (500v maximum). A minimum of one megohm to ground is required prior to applying power to these components. Perform all of the manufacturer's recommended prepower on checks and tests. Once completed, restore power to one variable speed drive at a time. At this time perform all of the manufacturer's recommended power on checks and tests. If all indications and readings are normal, attempt to run the variable speed drive. Start with a low speed and increase speed gradually in 5-10 Hz steps, while watching for normal running indications. Do not attempt to operate the equipment without proper testing.