- Products
-
- VSD Wiki
- Contact us
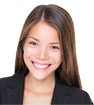
VSD manufacturers
sales@VariableSpeedDrive.co.za
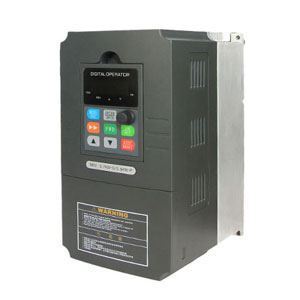
Most variable speed drive manufacturers require a reference to the neutral point of the winding, particularly for larger equipment. This connection serves as their primary "check" for unbalance in phase-phase and phase-ground circuits. As a side benefit, it keeps the VSD from accidentally damaging the machine winding insulation by over-voltaging the terminals by keeping the VSD and motor neutral at the same value.
Our cooling tower pumps are fixed speed but we have variable speed drives on the cooling tower fans. These do a good job of controlling the cooling tower supply temperature except in those installations where the cooling tower sump size is excessive (China). With the flow control valves on the individual exchanges, the variable speed drive may not be absolutely necessary, but the process temperature control works better if it doesn't have to deal with daytime to nighttime or storm induced variation in supply temperature.
Restoration of variable frequency drive that have been exposed to excessive moisture or have been in a flood pose a more difficult challenge. A typical variable speed drive contains a wide range of operating voltages and power supplies, complicated printed circuit boards and intricate control circuits. The severity of damage to the variable speed drive usually will depend on whether or not the variable speed drive was operating when the exposure occurred. The damage that occurs is most likely more severe if exposure occurs while the variable speed drive is operating. If the variable speed drive is exposed while it is not energized, the damage can be less severe but will usually be latent in nature. In either case, if any input line or internal power supply fuse is open or significant corrosion is present, contact the manufacturer for specific corrective measures.
Controlling pumps by variable speed drive improves production and site environment, and meet technics requirement completely. Integration of PLC control, Profibus technology and medium voltage variable speed drive leads to high automatization level, stable operation, easy operation and considerable energy saving.
Successful application of variable speed drive in Shenzhen Third Water Plant has enormous economic value in energy saving, technology innovation and downsize staff for high efficiency.
Successful application of variable speed drive in Shenzhen Third Water Plant has enormous economic value in energy saving, technology innovation and downsize staff for high efficiency.
When an application requires more current at a reduced speed, that means more heat and less cooling at the lower speeds. Most VSDs have limits to protect the VSD and consequently the motor. Too low a setting and there will be lot of trips. Too high a setting and there may be damage in high ambient temperatures.
If the pump has to operate at its max HP, the 125% may not be enough given the losses (excess current) required by the variable speed drive, especially with long feeders. In addition, noise from other high frequency devices like other variable speed drives, arc welders, etc can cause problems with the variable speed drive as well as the variable speed drive causing other problems on the electrical service. A line reactor or filter may be required there also. The lower the carrier frequency is, typically 2 KHz to 4 KHz, the noisier the motor but less losses and more efficient. The higher the carrier frequency, the quieter the motor operation but greater loses and more line current.
If the pump has to operate at its max HP, the 125% may not be enough given the losses (excess current) required by the variable speed drive, especially with long feeders. In addition, noise from other high frequency devices like other variable speed drives, arc welders, etc can cause problems with the variable speed drive as well as the variable speed drive causing other problems on the electrical service. A line reactor or filter may be required there also. The lower the carrier frequency is, typically 2 KHz to 4 KHz, the noisier the motor but less losses and more efficient. The higher the carrier frequency, the quieter the motor operation but greater loses and more line current.
At present, competition is very intense. The key is cost. Power consumption of motor accounts for 30% of cost. Motor driving fan is a big part. So it is very important to reduce consumption of motor. Today, phenomenon of "large horse drives small dolly" is serious. If technology of variable speed is adopted, it not only satisfies production requirement but also saves energy. Meanwhile, variable speed drive saves a lot of energy source and improves efficiency for plant. After innovation with variable speed drive, energy saving rate is in 30-50%. The investment usually recovers in one or two years.
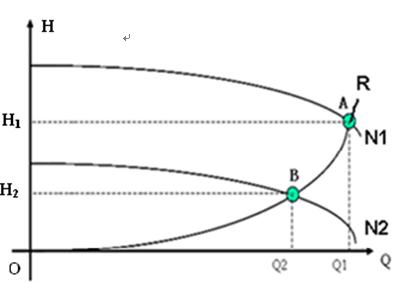
If 100% speed -100% flow -100% pressure-100% output power,there is: 80% speed- 80%flow- 64% pressure- 51% output power. Namely, in variable speed state, when flow reduces 20%, shaft power reduces 49%. That is the reason why variable speed drive has a considerable energy saving effect.
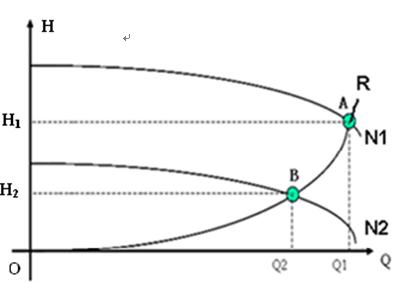
If 100% speed -100% flow -100% pressure-100% output power,there is: 80% speed- 80%flow- 64% pressure- 51% output power. Namely, in variable speed state, when flow reduces 20%, shaft power reduces 49%. That is the reason why variable speed drive has a considerable energy saving effect.
This article aimed to evaluate the uniformity of distribution and water depth applied with a center pivot irrigation systems according to the change in speed of rotation of set irrigation motor pump with a variable speed drive and the effect of the position of the lateral line in these parameters. Three positions of lines of collecting water were tested: incline of 3.45%, level and slope of 11.78%. The experimental design was completely randomized, with three replications made at each position tested. Analysis of variance was applied followed by Tukey test. Thee average value of the coefficient of uniformity of Heermann e Hein was 88.85%, describing the uniformity of water distribution as good. The mean weighed depth of irrigation applied was 5.71 mm, varying significantly within each test (5%) between the positions of slope versus incline and level. It was concluded that the position of the lateral line influenced significantly in the rotation of the set irrigation pump by variable speed drive, water depth applied and energy consumption. However, in the values of uniformity of water distribution there was no difference.
Variable speed drive sets speeds of 5 stages according to above table and speeds are required to be adjusted. Lowest speed of fan is set 10Hz temporarily and it is variable speed drive acceleration time is 46s (0~50Hz), no requirement for deceleration time. Variable speed drive should meet requirement of accelerating during deceleration.
Metal mixer of the steel plant uses a variable speed drive to control speed. The variable speed drive is high-high voltage source drive. Its main data is following: capacity is 1050KVA, rated output current is 105A, input frequency 45Hz~55Hz, rated input voltage 6000V, allowable voltage vibration -10%~10%, input power factor ≥0.96, output frequency 0~50Hz (speed adjustment range 0~100%), variable speed drive efficiency ≥98% (not including transformer), frequency resolution is 0.01Hz, stepless speed adjustment, overload capacity: 120% for 1min and 150% immediately. Acceleration time and deceleration time are set as per technics requirement.
Metal mixer of the steel plant uses a variable speed drive to control speed. The variable speed drive is high-high voltage source drive. Its main data is following: capacity is 1050KVA, rated output current is 105A, input frequency 45Hz~55Hz, rated input voltage 6000V, allowable voltage vibration -10%~10%, input power factor ≥0.96, output frequency 0~50Hz (speed adjustment range 0~100%), variable speed drive efficiency ≥98% (not including transformer), frequency resolution is 0.01Hz, stepless speed adjustment, overload capacity: 120% for 1min and 150% immediately. Acceleration time and deceleration time are set as per technics requirement.
The variable speed drives of degree of protection IP20 are designed, as a standard, for installation in electrical cabinets. During the VSD installation, both the installation and the safety instructions as well as the variable speed drive specifications must be complied with.
- To avoid serious physical injury or considerable damage to property, only qualified staff may work on the variable speed drive.
- During assembly, make sure that no foreign particles (e.g. chips, dust, wires, screws, tools) can get inside the variable speed drive. Otherwise there is the risk of short circuits and fire.
- The variable speed drive complies with protection class IP20 only if the covers, components and terminals are mounted properly.
- Overhead Installation or installation in horizontal position is not permissible.
In order to fully ensure the system reliability, a bypass device is configured with the medium voltage variable speed drive. When the medium voltage variable speed drive operates abnormally, it will stop and the motor may be manually switched to be driven directly by the power supply. The bypass circuit is composed of 3 medium voltage disconnect switches QS1, QS2 and QS3 (see the fig.6 in which QF is the original medium voltage switch). It is required that QS2 and QS3 may not be closed simultaneously and they are interlocked mechanically. When the motor is driven by medium voltage variable speed drive, QS1 and QS2 are closed and QS3 is open; and when the motor is driven by the power, QS3 is closed and QS1 and QS2 are open.
Fig.6 bypass circuit
In order to protect from medium voltage variable speed drive failure, the variable speed drive is interlocked with the 6kV switch QF. Once medium voltage variable speed drive fails, medium voltage variable speed drive will make QF switched off. It is required that the user makes suitable reform to the switching circuit. When the bypass circuit is acted, medium voltage variable speed drive will allow QF switch-on and cancel the switch off signal to enable the motor to start with the power through QF switching on.
To ensure safe operation of the generator unit, the reserved cycling pump is required to operate automatically under the operation mode of single cycling pump with variable speed drive, when variable speed drive fails and QF switches off. To adapt the improvement of automation level of cycling pump system after reform with variable speed drive, the outlet water valve is also interlocked for automatic control. The function of the valve interlock is: During the pump starts and its speed increases, the pump outlet water pressure increases gradually, and when the pressure is greater than the "minimum outlet water pressure for opening valve", the valve begins to open until to open fully. When the pump stops, the valve will close simultaneously. If the valve opens not completely for various reasons when the pump starts, "valve not open fully" will be displayed. If the valve closes not completely when the pump stops, "valve not close fully" will be displayed. Thus, during starting and stopping the pump, the personnel on duty need not to perform any operation to the valve and thus, not only operation miss will decrease but also the shock to the pipe network during opening valve and closing valve will be very small.
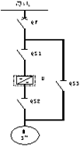
Fig.6 bypass circuit
In order to protect from medium voltage variable speed drive failure, the variable speed drive is interlocked with the 6kV switch QF. Once medium voltage variable speed drive fails, medium voltage variable speed drive will make QF switched off. It is required that the user makes suitable reform to the switching circuit. When the bypass circuit is acted, medium voltage variable speed drive will allow QF switch-on and cancel the switch off signal to enable the motor to start with the power through QF switching on.
To ensure safe operation of the generator unit, the reserved cycling pump is required to operate automatically under the operation mode of single cycling pump with variable speed drive, when variable speed drive fails and QF switches off. To adapt the improvement of automation level of cycling pump system after reform with variable speed drive, the outlet water valve is also interlocked for automatic control. The function of the valve interlock is: During the pump starts and its speed increases, the pump outlet water pressure increases gradually, and when the pressure is greater than the "minimum outlet water pressure for opening valve", the valve begins to open until to open fully. When the pump stops, the valve will close simultaneously. If the valve opens not completely for various reasons when the pump starts, "valve not open fully" will be displayed. If the valve closes not completely when the pump stops, "valve not close fully" will be displayed. Thus, during starting and stopping the pump, the personnel on duty need not to perform any operation to the valve and thus, not only operation miss will decrease but also the shock to the pipe network during opening valve and closing valve will be very small.
The typical variable speed drive operator interface provides a means for an operator to start & stop the motor & adjust the operating speed. Additional operator control functions might include reversing & switching between manual speed adjustment & automatic control from an external process control signal. The operator interface often includes an alphanumeric display and/or indication lights & meters to provide information about the operation of the variable speed drive. When mounted within another enclosure, a remote operator keypad & display may be cable-connected & mounted a short distance from the controller.
Most small variable speed drives are mounted in rack slots or on a DIN rail. The clips for mounting to the DIN rail are usually built into the fins of the heat sink to which the variable speed drive is mounted. This makes them easily installable in control cabinets. Larger variable speed drive units usually have through-hole mounting to accommodate individual fasteners. The fastening method should be adequate to support the weight of the variable speed drive & allow the free flow of air across the heat sink; airflow in some applications is aided by a cooling fan.
Mount the variable speed drive near the motor. Excessive cable length between the variable speed drive & the motor can result in extremely high voltage spikes at the motor leads. It's important to verify the maximum cable distance stated in the variable speed drive specifications, when you are installing variable speed drives onto AC induction motors. Excessive voltages can reduce the expected life of the insulation system, especially non-inverter-duty motors.
Line reactors stabilize the current waveform on the input side of a variable speed drive, reducing harmonic distortion & the burden on upstream electrical equipment. Harmonics are high-frequency voltage & current distortions within the power system normally caused by nonlinear loads that don't have a constant current draw, but rather draw current in pulses. Variable speed drives create harmonics when they convert AC to DC & DC back to AC.
In selecting a variable speed drive, consideration must be given to the load characteristics of the driven machinery. The three basic load categories can be summarized as follows:
- Constant-torque loads require a constant motor torque throughout the operational speed range.
- Loads of these types are essentially friction loads such as traction drives & conveyors.
- Variable-torque loads require much lower torque at low speeds than at high speeds. Loads that exhibit variable torque characteristics include centrifugal fans, pumps, & blowers.
- Shock (impact) loads require a motor to operate at normal load conditions followed by a sudden, large load applied to the motor. An example would be the sudden shock load that results from engaging a clutch that applies a large load to the motor (as it would during a hard start). This current spike could cause the variable speed drive to trip as a result an excessive motor current fault.
Here is the QUIZ about variable speed drives:
1. List the common basic control function of an electronic variable speed drive.
2. What is the preferred method for altering the speed of a squirrel-cage induction motor?
3. State the prime function of each of the following parts of a variable speed drive: (a) converter, (b) DC bus, (c) inverter, (d) control logic.
4. Explain how it's possible for a variable speed drive to operate a three-phase motor from a single phase power source.
5. Calculate the average DC bus voltage for a line volt age of 230 V AC.
6. Which component is the main energy storage element of the DC bus?
7. What types of transistor are currently used in the inverter section of a variable speed drive?
1. List the common basic control function of an electronic variable speed drive.
2. What is the preferred method for altering the speed of a squirrel-cage induction motor?
3. State the prime function of each of the following parts of a variable speed drive: (a) converter, (b) DC bus, (c) inverter, (d) control logic.
4. Explain how it's possible for a variable speed drive to operate a three-phase motor from a single phase power source.
5. Calculate the average DC bus voltage for a line volt age of 230 V AC.
6. Which component is the main energy storage element of the DC bus?
7. What types of transistor are currently used in the inverter section of a variable speed drive?
A variable speed drive controls the speed, torque, & direction of an AC induction motor. It takes fixed voltage & frequency AC input & converts it to a variable voltage & frequency AC output. Below Fig shows the block diagram of a typical three phase variable speed drive controller.
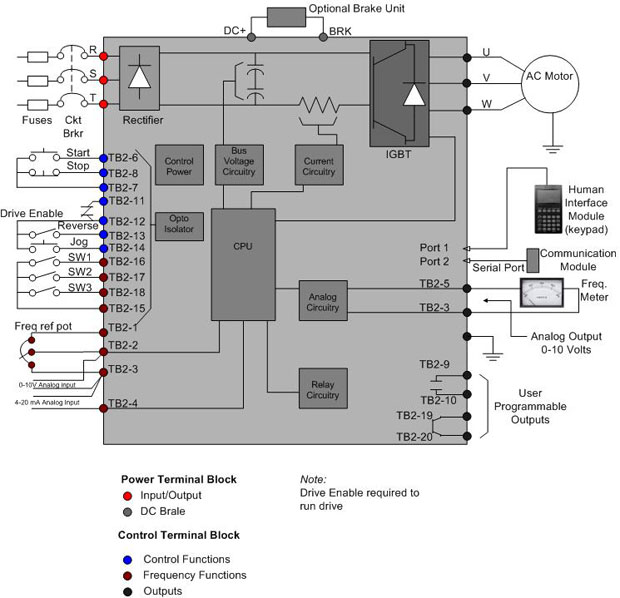
The function of each block is as follows:
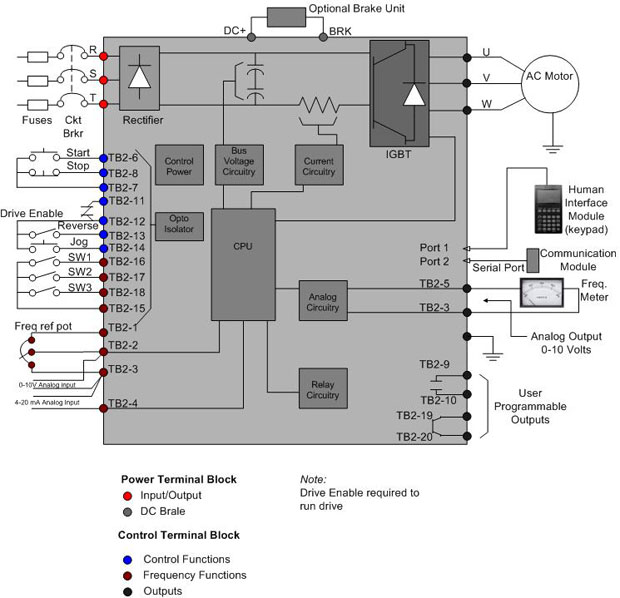
The function of each block is as follows:
- Converter: A full-wave rectifier that converts the applied AC to DC.
- DC bus: Also referred to as a DC link, connects the rectifier output to the input of the inverter. The DC bus functions as a filter to smooth the uneven, rippled output to ensure that the rectified output resembles as closely as possible pure DC.
- Inverter: The inverter takes the filtered DC from the DC bus & converts it into a pulsating DC waveform. By controlling the output of the inverter, the pulsating DC waveform can simulate an AC waveform at different frequencies.
- Control logic: The control logic system generates the necessary pulses used to control the firing of the power semiconductor devices such as SCRs & transistors. Fairly involved control circuitry coordinates the switching of power devices, typically through a control board that dictates the firing of power components in the proper sequence. An embedded microprocessor is used for all internal logic & decision requirements.
Proper speed control means that you need to vary both the motor voltage and frequency to control slip and keep it in a sweet zone in relation to the actual rotation speed. This is what Variable Speed Drives do. A fly in the ointment however is that for single phase induction motors this idea does not really work. You noted that i wrote earlier that the stator windings create a rotating magnetic field. Only you won't get rotation with just one phase, you get a pulsing voltage only. For this reason single phase motors artificially create a second phase to create the rotation. This second phase can be created in many ways using auxiliary windings and phase shift capacitors or coils. Combining a variable speed drive and a single phase motor is at best a horrible kludge and usually does not even begin to work. All proper variable speed drive controlled induction motors are 3 phase, as are the outputs of the variable speed drives. 3 phase shifted voltages is the minimum required to create a rotating field.
Back to single phase motors. In certain kinds of application, you can skip variable speed drives and simply control the motor by controlling the effective stator voltage using a triac or thyristor or whatever. This does nothing to the supply frequency, which is the standard 50/60 Hz all the time. So what is controlled is the amount of slip, by crude indirect torque control by stator voltage. If the load curve is monotonously increasing and sufficiently steep, the rotation speed will follow the stator voltage. Not linearly and not with world class dynamics, but it will follow. Now it happens that a fan is typically this kind of load and for that reason this simple scheme works quite OK for most fans.
Back to single phase motors. In certain kinds of application, you can skip variable speed drives and simply control the motor by controlling the effective stator voltage using a triac or thyristor or whatever. This does nothing to the supply frequency, which is the standard 50/60 Hz all the time. So what is controlled is the amount of slip, by crude indirect torque control by stator voltage. If the load curve is monotonously increasing and sufficiently steep, the rotation speed will follow the stator voltage. Not linearly and not with world class dynamics, but it will follow. Now it happens that a fan is typically this kind of load and for that reason this simple scheme works quite OK for most fans.